Continuous Improvement
The concept of continuous improvement, also known as kaizen, posits that an organization can attain a competitive advantage by consistently and progressively enhancing its processes and operations at a rate superior to that of its rivals. This approach aims to position the organization as a market leader through sustained improvement efforts.
Continuous improvement has historically been associated with the implementation of lean principles, specifically in regards to the reduction of waste within processes. These principles were initially applied successfully in the automotive industry by Taiichi Ohno, Chief Engineer at Toyota, in the 1990s. However, over time, lean principles have been adapted and applied in a variety of business settings.
See answers below...
Continuous improvement and lean thinking are concepts that involve the development of a culture and mindset characterized by a focus on efficiency and continuous improvement. These ideas are not just isolated processes or techniques, but rather a way of approaching work and decision-making.
Six Sigma is not a Synonym for Lean
It is often assumed by business managers that the mere presence of a Six Sigma-trained employee within an organization signifies a readiness to implement continuous improvement and lean processes. However, this is a mistaken belief and it is not uncommon for organizations to wrongly claim they are lean simply due to having a Six Sigma-trained individual on staff. This assertion is erroneous.
Possession of a black belt qualification in six sigma denotes proficiency in various lean techniques, such as 5S, value stream mapping, and poka-yoke. These methods can be utilized as tools within the lean toolbox in order to effectively address specific issues or challenges as they arise.
As a mechanic has a variety of tools in their toolbox, such as socket sets, screwdrivers, and grease guns, a lean leader also has various tools available to them. However, it is important for both the mechanic and the lean practitioner to utilize the appropriate tool for the specific task at hand. For example, a mechanic would not use a screwdriver to remove a car wheel, just as a lean practitioner would not utilize six sigma for conducting a root cause analysis.
Prioritizing Cultural Change
Continuous improvement, as a concept, requires a continuous and ongoing effort in order to be effective. It is not a temporary or singular initiative, but rather a fundamental element of the organizational culture that must be embraced and implemented by all members of the company. Only through this consistent and comprehensive approach can the resulting changes and improvements be maintained and sustained over time.
At Liberty Point, we specialize in implementing continuous improvement as a philosophy through targeted change management programs. These programs range from short-term, high-impact projects that drive further improvement streams to long-term lean introduction programs aimed at inducing fundamental cultural change. Details of these programs are provided below:
Lean Culture Kick Start
The Lean Culture Kick Start program consists of an Introduction to Lean training course, which serves as a foundation for the following companywide lean project idea generation competition. During this competition, teams will gain an understanding of the principles of continuous improvement, including the identification of the 7 wastes, and then propose lean projects for the organization. The resulting lean strategy, determined by the competition's outcome, will be implemented for at least the next year. To view a Lean Culture Kick Start case study click here...
Waste Reduction Programs
These programs are geared towards addressing specific functions and departments within an organization where it has been identified that there is a need for increased efficiency. Basic continuous improvement training will be offered, but the main emphasis will be on a full Kaizen event reviewing the reason for change and conducting waste analysis and implementing appropriate lean tools and techniques to resolve persistent issues. These programs have a track record of effectively improving efficiency and providing tangible cost savings in a relatively short timeframe.
Fire Extinguisher Projects
The primary goal of our Fire Extinguisher projects is to identify and solve a problem that has disrupted business operations and establish a long-term solution to prevent similar incidents from happening in the future. We will utilize continuous and lean methodologies as necessary, but the main focus is to quickly and efficiently restore normal operations for the company. After the situation has been resolved, a thorough analysis will be conducted to evaluate what was learned from the experience. This is not a simulated training scenario; this is the management and remedy of a real emergency situation.
Companywide Improvement
At Liberty Point, we have established Companywide Improvement programs to deliver a long-term shift towards a lean culture. To oversee this initiative, we will assign a dedicated Continuous Improvement Manager on a full-time basis. In order to ensure the success of this program, it is essential that upper management within the organization fully supports and embraces the forthcoming changes, which will be assessed during the due diligence phase. Upon approval, a comprehensive project plan will be developed and implemented.
To initiate a conversation about implementing continuous improvement within your organization and learn about the assistance Liberty Point can provide, please reach out to us through the contact details below.
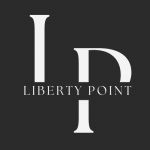
Copyright@libertypoint.io 2022
Continuous Improvement
See answers below...
The concept of continuous improvement, also known as kaizen, posits that an organization can attain a competitive advantage by consistently and progressively enhancing its processes and operations at a rate superior to that of its rivals. This approach aims to position the organization as a market leader through sustained improvement efforts.
Continuous improvement has historically been associated with the implementation of lean principles, specifically in regards to the reduction of waste within processes. These principles were initially applied successfully in the automotive industry by Taiichi Ohno, Chief Engineer at Toyota, in the 1990s. However, over time, lean principles have been adapted and applied in a variety of business settings.
Continuous improvement and lean thinking are concepts that involve the development of a culture and mindset characterized by a focus on efficiency and continuous improvement. These ideas are not just isolated processes or techniques, but rather a way of approaching work and decision-making.
Six Sigma is not a Synonym for Lean
It is often assumed by business managers that the mere presence of a Six Sigma-trained employee within an organization signifies a readiness to implement continuous improvement and lean processes. However, this is a mistaken belief and it is not uncommon for organizations to wrongly claim they are lean simply due to having a Six Sigma-trained individual on staff. This assertion is erroneous.
Possession of a black belt qualification in six sigma denotes proficiency in various lean techniques, such as 5S, value stream mapping, and poka-yoke. These methods can be utilized as tools within the lean toolbox in order to effectively address specific issues or challenges as they arise.
As a mechanic has a variety of tools in their toolbox, such as socket sets, screwdrivers, and grease guns, a lean leader also has various tools available to them. However, it is important for both the mechanic and the lean practitioner to utilize the appropriate tool for the specific task at hand. For example, a mechanic would not use a screwdriver to remove a car wheel, just as a lean practitioner would not utilize six sigma for conducting a root cause analysis.
Prioritizing Cultural Change
Continuous improvement, as a concept, requires a continuous and ongoing effort in order to be effective. It is not a temporary or singular initiative, but rather a fundamental element of the organizational culture that must be embraced and implemented by all members of the company. Only through this consistent and comprehensive approach can the resulting changes and improvements be maintained and sustained over time.
At Liberty Point, we specialize in implementing continuous improvement as a philosophy through targeted change management programs. These programs range from short-term, high-impact projects that drive further improvement streams to long-term lean introduction programs aimed at inducing fundamental cultural change. Details of these programs are provided below:
Lean Culture Kick Start
The Lean Culture Kick Start program consists of an Introduction to Lean training course, which serves as a foundation for the following companywide lean project idea generation competition. During this competition, teams will gain an understanding of the principles of continuous improvement, including the identification of the 7 wastes, and then propose lean projects for the organization. The resulting lean strategy, determined by the competition's outcome, will be implemented for at least the next year. To view a Lean Culture Kick Start case study click here...
Waste Reduction Programs
These programs are geared towards addressing specific functions and departments within an organization where it has been identified that there is a need for increased efficiency. Basic continuous improvement training will be offered, but the main emphasis will be on a full Kaizen event reviewing the reason for change and conducting waste analysis and implementing appropriate lean tools and techniques to resolve persistent issues. These programs have a track record of effectively improving efficiency and providing tangible cost savings in a relatively short timeframe.
Fire Extinguisher Projects
The primary goal of our Fire Extinguisher projects is to identify and solve a problem that has disrupted business operations and establish a long-term solution to prevent similar incidents from happening in the future. We will utilize continuous and lean methodologies as necessary, but the main focus is to quickly and efficiently restore normal operations for the company. After the situation has been resolved, a thorough analysis will be conducted to evaluate what was learned from the experience. This is not a simulated training scenario; this is the management and remedy of a real emergency situation.
Company Wide Improvement
At Liberty Point, we have established Companywide Improvement programs to deliver a long-term shift towards a lean culture. To oversee this initiative, we will assign a dedicated Continuous Improvement Manager on a full-time basis. In order to ensure the success of this program, it is essential that upper management within the organization fully supports and embraces the forthcoming changes, which will be assessed during the due diligence phase. Upon approval, a comprehensive project plan will be developed and implemented.
Lean Culture Kick Start
The Lean Culture Kick Start program consists of an Introduction to Lean training course, which serves as a foundation for the following companywide lean project idea generation competition. During this competition, teams will gain an understanding of the principles of continuous improvement, including the identification of the 7 wastes, and then propose lean projects for the organization. The resulting lean strategy, determined by the competition's outcome, will be implemented for at least the next year. To view a Lean Culture Kick Start case study click here...
Waste Reduction Programs
These programs are geared towards addressing specific functions and departments within an organization where it has been identified that there is a need for increased efficiency. Basic continuous improvement training will be offered, but the main emphasis will be on a full Kaizen event reviewing the reason for change and conducting waste analysis and implementing appropriate lean tools and techniques to resolve persistent issues. These programs have a track record of effectively improving efficiency and providing tangible cost savings in a relatively short timeframe.
Fire Extinguisher Projects
The primary goal of our Fire Extinguisher projects is to identify and solve a problem that has disrupted business operations and establish a long-term solution to prevent similar incidents from happening in the future. We will utilize continuous and lean methodologies as necessary, but the main focus is to quickly and efficiently restore normal operations for the company. After the situation has been resolved, a thorough analysis will be conducted to evaluate what was learned from the experience. This is not a simulated training scenario; this is the management and remedy of a real emergency situation.
Company Improvement
At Liberty Point, we have established Companywide Improvement programs to deliver a long-term shift towards a lean culture. To oversee this initiative, we will assign a dedicated Continuous Improvement Manager on a full-time basis. In order to ensure the success of this program, it is essential that senior management within the organization fully support, embrace, and buy-in to the forthcoming changes, which will be assessed during the due diligence phase. Upon approval, a comprehensive project and resource plan will be developed and implemented.
To initiate a conversation about implementing continuous improvement within your organization and learn about the assistance Liberty Point can provide, please reach out to us through the contact details below.
Copyright@libertypoint.io 2022